Addressing Challenges In Automated Visual Inspection Of Lyophilized Vials
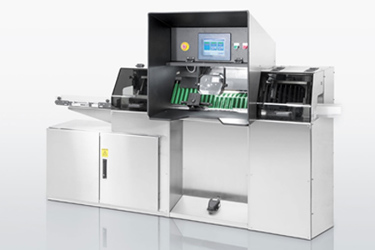
Table of Contents
Image Acquisition Challenges in Automated Visual Inspection of Lyophilized Vials
High-quality image acquisition is the foundation of successful automated visual inspection. Several factors can significantly impact the quality of images captured, leading to inaccuracies in defect detection.
Lighting and Shadow Effects
Inconsistencies in lighting are a major hurdle. Variations in illumination create shadows that can obscure defects, leading to false negatives – the system missing actual defects.
- Variations in vial surface reflectivity: Different vial materials and surface finishes reflect light differently, creating uneven illumination and shadowing.
- Difficulties in uniform illumination across the vial: Achieving consistent illumination across the entire vial surface is challenging, especially with curved surfaces and variations in fill level.
- The impact of vial orientation on shadow formation: The angle of the light source relative to the vial significantly impacts shadow formation, necessitating precise control of lighting and vial positioning.
Advanced lighting techniques, such as structured lighting or multi-angle illumination, can mitigate these issues by providing more uniform and shadow-free images.
Particle Detection and Differentiation
Distinguishing between actual defects, such as particulate matter, and harmless variations, such as air bubbles or crystallization, presents a significant challenge. This requires sophisticated image processing algorithms capable of subtle differentiation.
- Challenges in differentiating between different types of particles: Particles vary in size, shape, color, and reflectivity, making accurate classification difficult.
- The need for high-resolution imaging to detect small particles: Detecting small particles requires high-resolution cameras and powerful image processing capabilities.
- Developing algorithms robust to variations in vial fill levels: The fill level within the vial can affect the appearance of defects, demanding algorithms that are insensitive to these variations.
Machine learning algorithms, particularly those based on deep learning, offer promising solutions for enhancing particle detection and classification accuracy by learning from large datasets of images.
Algorithm Development and Optimization for Automated Visual Inspection of Lyophilized Vials
The development and optimization of robust algorithms are critical for the success of automated visual inspection systems.
Algorithm Accuracy and False Positives/Negatives
Striking a balance between high accuracy and minimizing both false positives (rejecting good vials) and false negatives (accepting defective vials) is crucial. This impacts both efficiency and cost.
- The need for robust machine learning models trained on diverse datasets: Algorithms need to be trained on large and diverse datasets representing a wide range of vials, defects, and lighting conditions.
- Balancing sensitivity and specificity in defect detection: The system needs to be sensitive enough to detect even small defects while being specific enough to avoid false positives.
- Regular algorithm retraining and updates to maintain accuracy: As manufacturing processes or vial characteristics change, regular retraining is necessary to maintain algorithm accuracy and adapt to those variations.
Ongoing monitoring and evaluation of algorithm performance are key to minimizing errors and optimizing accuracy.
Computational Speed and Processing Power
Real-time inspection of lyophilized vials requires algorithms that can process images rapidly. This demands significant computing power and optimized algorithms.
- The need for optimized algorithms to reduce processing time: Efficient algorithms are critical for minimizing inspection time and maximizing throughput.
- The use of specialized hardware (e.g., GPUs) to accelerate processing: Graphics processing units (GPUs) can significantly speed up image processing compared to CPUs.
- Balancing speed and accuracy requirements: There's a trade-off between speed and accuracy; optimization involves finding the right balance for the specific application.
Utilizing parallel processing techniques and hardware acceleration can help achieve real-time performance without sacrificing accuracy.
Regulatory Compliance and Validation for Automated Visual Inspection of Lyophilized Vials
Regulatory compliance and validation are paramount for any automated visual inspection system used in pharmaceutical manufacturing.
Meeting Regulatory Standards
Automated visual inspection systems must meet stringent regulatory requirements, such as 21 CFR Part 11 in the US, regarding data integrity and traceability.
- Validation of the entire system, including hardware and software: Rigorous validation procedures are needed to demonstrate that the system consistently meets its performance specifications.
- Implementing robust quality control procedures: Continuous quality control ensures the system remains accurate and reliable over time.
- Maintaining comprehensive audit trails: Detailed records of all inspections, system configurations, and maintenance activities are vital for regulatory compliance.
Thorough documentation and validation are essential to meet regulatory requirements and build confidence in the system's reliability.
Data Management and Reporting
Efficient data management and reporting are essential for traceability and compliance.
- Storing and archiving inspection data securely: Inspection data needs to be stored securely and accessibly for future reference and audits.
- Generating reports that meet regulatory requirements: Reports must contain all necessary information for compliance and analysis.
- Integrating with existing enterprise systems: Seamless integration with existing systems streamlines data management and reporting workflows.
Proper data management ensures traceability and efficient regulatory compliance.
Conclusion
Automated visual inspection of lyophilized vials offers significant advantages over manual methods, providing speed, accuracy, and consistency. However, successfully implementing this technology requires overcoming challenges related to image acquisition, algorithm development, and regulatory compliance. Addressing these challenges through advanced image processing, robust algorithms, thorough validation processes, and careful consideration of regulatory standards is crucial. Investing in and implementing advanced solutions for automated visual inspection of lyophilized vials is vital for ensuring product safety and meeting stringent regulatory standards. Companies should prioritize research and development in this area to achieve higher accuracy and efficiency in their quality control processes. The future of pharmaceutical quality control depends on further advancements in this critical technology.
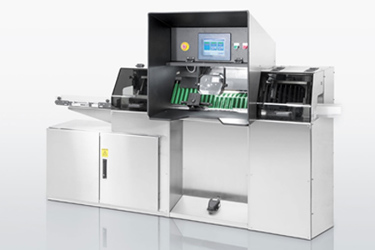
Featured Posts
-
China Trade Talks Trump Administration Targets Tariff Relief And Rare Earths
May 11, 2025 -
The Unexpected Success Of The Fake Henry Cavill Marvel Cyclops Trailer
May 11, 2025 -
Could Payton Pritchard Win Sixth Man Of The Year Analyzing His Historic Season
May 11, 2025 -
Boris And Carrie Johnsons Easter Message A Rare Glimpse Of Their Son
May 11, 2025 -
Who Could Be The Next Pope Potential Candidates And Predictions
May 11, 2025