Automated Visual Inspection Of Lyophilized Vials: Challenges And Solutions
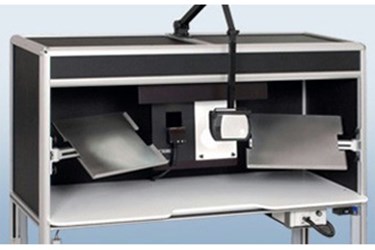
Table of Contents
1. Introduction:
The demand for lyophilized pharmaceuticals is soaring, driving the need for faster, more accurate quality control methods. Manual visual inspection of lyophilized vials, while traditionally employed, suffers from inherent limitations. Human error, subjectivity in defect assessment, and low throughput significantly impact production efficiency and lead to increased costs. This article addresses these challenges by examining the benefits of transitioning to automated visual inspection systems, leveraging advanced imaging techniques and artificial intelligence to ensure superior product quality and increased profitability.
2. Main Points:
H2: Challenges in Manual Visual Inspection of Lyophilized Vials:
H3: Subjectivity and Variability: Human inspectors face inherent limitations in consistently identifying subtle defects in lyophilized vials. The interpretation of cracks, particulate matter, discoloration, and other visual imperfections varies significantly between individuals.
- Examples of subjective defects: Determining the severity of a crack, differentiating between acceptable and unacceptable levels of particulate matter, and assessing the uniformity of cake appearance.
- Impact of human factors: Fatigue, experience level, and even lighting conditions influence an inspector's judgment, leading to inconsistencies in quality control. This subjectivity translates to variability in defect classification and potential for overlooking critical flaws.
H3: Low Throughput and Bottlenecks: Manual inspection is incredibly time-consuming. Inspecting thousands of vials daily is labor-intensive and slow, creating a significant bottleneck in the production process.
- Inspection time per vial: A conservative estimate might place manual inspection time at 15-30 seconds per vial, drastically impacting overall production capacity. For high-volume manufacturing, this translates to significant delays and reduced output.
- Limitations in high-volume environments: Manual inspection struggles to keep up with the demands of modern high-speed lyophilization lines, creating a major constraint on overall production efficiency.
H3: High Costs Associated with Manual Inspection: Manual visual inspection involves substantial labor costs. The risk of human error also contributes significantly to potential product recalls and associated financial losses.
- Labor cost breakdown: Consider the cost of employing and training personnel, including wages, benefits, and training expenses. This adds up considerably, especially when considering the volume of vials requiring inspection.
- Financial impact of recalls: A single recall due to undetected defects can be financially devastating, outweighing the initial investment in automated systems many times over. This cost includes legal fees, product disposal, and damage to brand reputation.
H2: Solutions Offered by Automated Visual Inspection Systems:
H3: Advanced Imaging Techniques: Automated visual inspection systems leverage advanced imaging technologies to overcome the limitations of manual inspection. High-resolution cameras, coupled with sophisticated machine vision algorithms, enable detailed analysis of each vial. Different lighting techniques further enhance defect detection.
- Advantages of various techniques: Bright field illumination is effective for overall vial assessment, while dark field illumination excels at highlighting particulate matter and subtle cracks. Hyperspectral imaging can even identify chemical variations within the lyophilized cake.
- Advanced imaging technologies: 3D imaging provides a comprehensive view of the vial’s surface, allowing for the detection of subtle irregularities that might be missed with 2D imaging.
H3: Artificial Intelligence (AI) and Machine Learning (ML) in Defect Detection: AI and ML algorithms are trained on extensive datasets of images representing various defects. These algorithms learn to recognize patterns and anomalies, providing faster and more accurate defect detection compared to human inspectors.
- Algorithm training and defect recognition: Sophisticated algorithms are trained to identify various defects, including cracks, delamination, particulate matter, and variations in cake appearance.
- Self-learning algorithms and continuous improvement: Modern AI systems are capable of continuous learning and improvement. The more data they process, the more accurate and efficient they become in detecting defects.
H3: Integration with Existing Production Lines: Modern automated visual inspection systems are designed for seamless integration into existing lyophilization lines. This minimizes disruption and maximizes the efficiency gains from automation.
- Integration options: Systems can be integrated at various points in the production line, depending on the specific needs and existing infrastructure. They can be easily integrated with existing conveyor systems and other automation technologies.
- Increased Overall Equipment Effectiveness (OEE): Automated systems improve the overall equipment effectiveness by reducing downtime associated with manual inspection and improving the consistency of quality control processes.
H2: Benefits of Implementing Automated Visual Inspection:
H3: Improved Quality Control: Automated visual inspection significantly reduces human error, leading to more consistent and reliable quality control. This results in a higher level of confidence in the final product quality.
- Improved consistency and reliability: Automated systems deliver consistent results regardless of human factors like fatigue or experience.
- Reduced product recalls: Minimizing defects through improved detection leads to fewer product recalls and significantly reduces financial losses.
H3: Increased Efficiency and Throughput: Automation dramatically increases inspection speed, enabling significantly higher throughput compared to manual inspection.
- Improved throughput and reduced inspection time: Automated systems can inspect hundreds or even thousands of vials per hour, increasing overall production capacity.
- Impact on production capacity: This boost in production capacity allows manufacturers to meet increased demands and optimize their production schedules.
H3: Reduced Costs and Return on Investment (ROI): While there is an initial investment in the automated systems, the long-term cost savings from reduced labor, reduced product waste from recalls, and higher throughput create a strong return on investment.
- Potential ROI calculation: A detailed cost-benefit analysis can showcase substantial savings through reduced labor costs, minimized recalls, and increased production volume, resulting in a positive ROI within a short timeframe.
- Long-term benefits and cost-effectiveness: The long-term cost-effectiveness of automated visual inspection becomes apparent as the system continues to deliver consistent, accurate results, year after year.
3. Conclusion:
Manual visual inspection of lyophilized vials presents significant challenges including subjectivity, low throughput, and high costs. Automated visual inspection systems offer a compelling solution, leveraging advanced imaging techniques, AI, and seamless integration to address these challenges effectively. The benefits – improved quality control, increased efficiency, reduced costs, and enhanced overall product quality – make the transition to automation a strategic imperative for pharmaceutical manufacturers. Optimize your automated visual inspection of lyophilized vials today and contact a supplier to explore the solutions available to improve your lyophilized vial production processes and enhance your quality control. Invest in automated visual inspection for enhanced lyophilized vial quality control and a stronger bottom line.
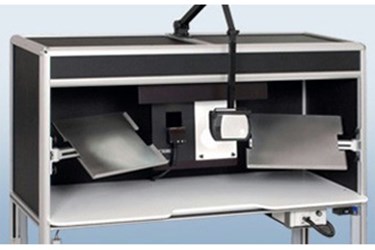
Featured Posts
-
Analyzing Apples Influence On Googles Market Share
May 11, 2025 -
Cooyahs Grand Slam Track Collection A New Line Of Athletic Apparel
May 11, 2025 -
Yankees Magazine Examining Aaron Judges Path To A Historic 2024
May 11, 2025 -
Gazas Struggle For Survival Hunger Disease And Crime In A Besieged Territory
May 11, 2025 -
Allegations Of Prince Andrews Actions With Underage Girl Emerge In Leaked Footage
May 11, 2025