Challenges And Advancements In Automated Visual Inspection Of Lyophilized Vials
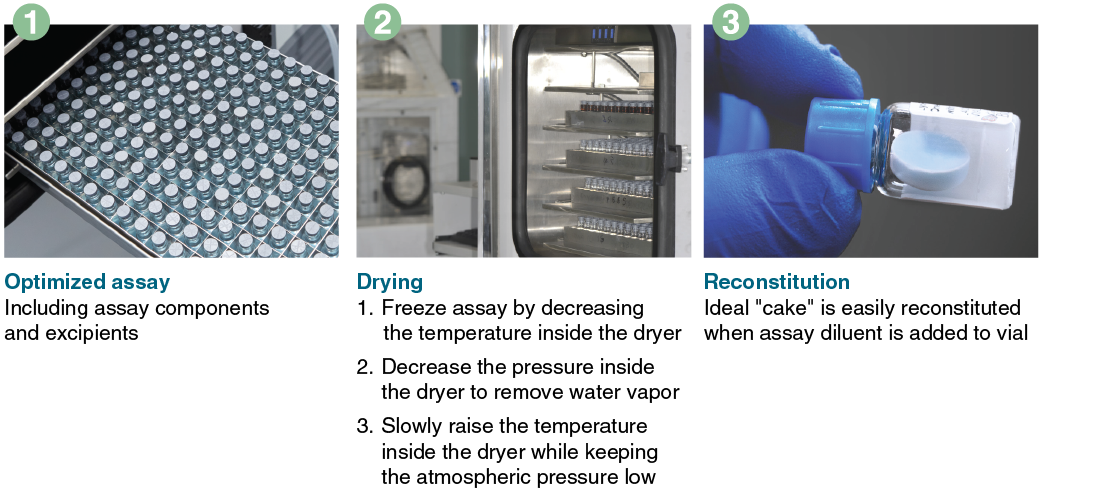
Table of Contents
Challenges in Automated Visual Inspection of Lyophilized Vials
The automated visual inspection of lyophilized vials presents several unique challenges that demand innovative solutions. These challenges stem from the inherent variability of the lyophilization process and the complexities of imaging the product within its glass container.
Variability in Lyophilized Product Appearance
The lyophilization process, while crucial for preserving drug stability, can introduce variations in the appearance of the resulting lyophilized cake. These variations complicate automated defect detection.
- Subtle Cracks: Microscopic cracks or fissures in the lyophilized cake can be difficult to differentiate from normal variations in the cake's structure. These subtle defects require high-resolution imaging and sophisticated algorithms for reliable detection.
- Variations in Vial Clarity and Color: Inconsistencies in the clarity and color of the glass vials themselves can interfere with image analysis. These variations can obscure defects or create false positives. Careful calibration and advanced image processing techniques are essential to compensate for this.
- Differences in Cake Shape and Size: The lyophilization process can lead to variations in the size and shape of the lyophilized cake. This variability necessitates algorithms capable of adapting to different cake morphologies to avoid misinterpretations. Adaptive image analysis and machine learning techniques are crucial in overcoming this challenge.
Dealing with Reflections and Shadows
The physical properties of glass vials and the lyophilized product itself contribute to the generation of reflections and shadows that severely hinder accurate image acquisition.
- Glare from Light Sources: Reflections from the curved surface of the vial and the lyophilized cake can create glare that obscures defects. Careful control of light sources and advanced lighting techniques are necessary to minimize this effect.
- Shadows Masking Imperfections: Shadows cast by the vial or the cake itself can mask cracks, particulate matter, or other imperfections, leading to missed defects. Optimized lighting and advanced image processing algorithms are essential to mitigate these issues.
- Advanced Lighting Techniques: Innovative lighting techniques, such as structured illumination and multispectral imaging, are being developed to improve the quality of images acquired during automated visual inspection. These techniques aim to reduce the impact of reflections and shadows while enhancing the visibility of defects.
High Throughput Demands and Speed vs. Accuracy
The pharmaceutical industry demands high-throughput automated visual inspection to keep pace with production requirements. Balancing the need for speed with the critical requirement for accurate defect detection presents a significant challenge.
- Speed vs. Accuracy Trade-off: Increasing the speed of inspection can compromise the accuracy of defect detection, potentially leading to the release of substandard products.
- Sophisticated Algorithms and Hardware: Meeting the demands of high-throughput inspection requires sophisticated algorithms and hardware capable of processing images rapidly and accurately.
- Minimizing False Positives and Negatives: A critical aspect of successful AVI is minimizing both false positives (incorrectly identifying a defect) and false negatives (missing actual defects). This requires carefully designed algorithms and rigorous validation processes.
Advancements in Automated Visual Inspection Technology for Lyophilized Vials
Despite the challenges, significant advancements in AVI technology are addressing these limitations and improving the accuracy, speed, and efficiency of automated visual inspection systems for lyophilized vials.
Improved Image Processing Algorithms
The application of advanced image processing algorithms, particularly those based on machine learning and deep learning, is significantly improving the accuracy of defect detection.
- AI-Powered Defect Recognition: Artificial intelligence (AI) powered systems are capable of learning to recognize subtle variations and defects that would be difficult for traditional algorithms to identify.
- Deep Learning for Improved Accuracy: Deep learning models, trained on extensive datasets of lyophilized vial images, are achieving superior accuracy in defect detection. These models can learn complex patterns and adapt to variations in product appearance.
- Enhanced Image Processing for Reflection Reduction: Improved image processing techniques are designed to reduce the impact of reflections and shadows, enhancing the clarity of images and improving defect detection accuracy.
Advanced Lighting and Imaging Techniques
Innovative lighting and imaging techniques are enhancing image quality, improving the visibility of subtle defects.
- Multispectral Imaging: Multispectral imaging captures information beyond the visible spectrum, providing additional data that can enhance defect detection.
- Structured Lighting for Enhanced Detail: Structured lighting techniques project patterns onto the lyophilized cake, enhancing surface detail visualization and improving the ability to detect subtle cracks or imperfections.
- Optimized Illumination for Reflection Minimization: Careful optimization of illumination parameters minimizes reflections and shadows, creating clearer and more accurate images for analysis.
Integration of Robotic Systems and Automation
The integration of robotic systems is streamlining the inspection process, boosting efficiency and reducing manual intervention.
- Automated Vial Handling: Automated vial handling and presentation systems reduce manual intervention, improving throughput and reducing the risk of human error.
- Integration with Production Lines: Integration with other automated systems enhances overall production efficiency and facilitates seamless workflow within the manufacturing process.
- Improved Throughput without Compromising Accuracy: Robotic automation improves throughput while maintaining high levels of accuracy in defect detection, optimizing both speed and quality control.
Conclusion
Automated visual inspection of lyophilized vials presents considerable challenges related to product variability, image acquisition difficulties, and throughput requirements. However, recent advancements in image processing algorithms, lighting techniques, and robotic automation are dramatically improving the accuracy, speed, and efficiency of AVI systems. By adopting these advancements, pharmaceutical companies can ensure the superior quality and safety of their lyophilized products, safeguarding patient health. Further research and development in automated visual inspection of lyophilized vials will remain crucial to meet the ever-increasing demand for high-quality, safe pharmaceuticals. Invest in the future of pharmaceutical quality control by exploring the latest advancements in automated visual inspection of lyophilized vials and its related technologies.
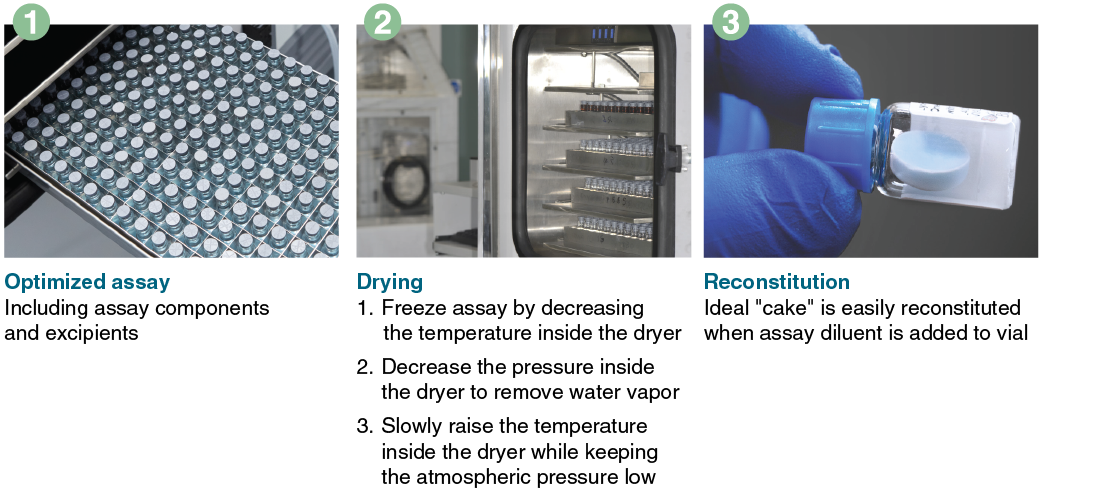
Featured Posts
-
One Indy Car Driver Out Of The 2025 Indy 500
May 11, 2025 -
Kieran Stevenson And Ipswich Town Looking Ahead
May 11, 2025 -
Yankees Diamondbacks Injury Update April 1st 3rd Games
May 11, 2025 -
Selena Gomez And Benny Blanco No First Dance At Wedding
May 11, 2025 -
Netherlands Plans Low Security Detention Centers For Asylum Seekers
May 11, 2025
Latest Posts
-
Chantal Ladesou Entretien Exclusif Et Revue De Carriere
May 12, 2025 -
L Humoriste Chantal Ladesou Ses Plus Grands Succes Et Ses Prochains Projets
May 12, 2025 -
Tout Savoir Sur Chantal Ladesou Filmographie Pieces De Theatre Et Vie Privee
May 12, 2025 -
Chantal Ladesou Une Longue Carriere Au Theatre Et Au Cinema
May 12, 2025 -
Chantal Ladesou Biographie Spectacles Et Actualites
May 12, 2025