Improving The Accuracy Of Automated Visual Inspection For Lyophilized Vials
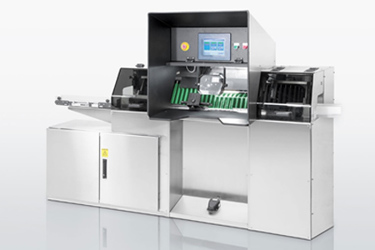
Table of Contents
Challenges in Current Automated Visual Inspection for Lyophilized Vials
Current Automated Visual Inspection for Lyophilized Vials systems, while offering significant advancements over manual inspection, still encounter hurdles in achieving perfect accuracy. These challenges stem from several key areas:
Difficulties in Defect Detection
Identifying subtle defects in lyophilized vials presents a significant challenge for current AVI systems. These defects, often microscopic, can significantly impact product quality and patient safety.
- Subtle Defects: Cracks in the vial, minute particulate matter within the lyophilized cake, and inconsistencies in fill level are notoriously difficult to detect reliably. The variations in these defects make consistent detection particularly challenging.
- Variability in Lighting and Presentation: Differences in lighting conditions and the way vials are presented to the inspection system can lead to both false positives (correctly functioning vials rejected) and false negatives (defective vials passing inspection). This necessitates careful control of lighting and vial positioning.
- Lyophilized Product Complexity: The inherent complexity of the lyophilized product morphology itself adds to the difficulty. The cake's structure and appearance can vary considerably depending on the formulation and lyophilization process, making consistent defect identification difficult.
- Need for Improved Image Processing Algorithms: Advanced algorithms are crucial to account for the inherent variations in vial appearance and cake morphology, improving the ability to distinguish between defects and natural variations.
- Limitations of Current Imaging Technologies: The resolution and depth of field of current imaging technologies often limit the ability to detect very small or deeply embedded defects. Higher resolution and improved depth of field are crucial for accurate detection.
Maintaining System Sensitivity and Specificity
Achieving the optimal balance between sensitivity (detecting all defects) and specificity (avoiding false positives) remains a critical challenge in AVI for lyophilized vials.
- The Sensitivity/Specificity Trade-off: A highly sensitive system will detect even minor variations, leading to a high rate of false positives and increased rejection of perfectly good vials. Conversely, a system prioritizing specificity might miss critical defects, risking patient safety and product quality.
- Cost of False Positives: False positives lead to significant waste due to the unnecessary rejection of acceptable vials, increasing manufacturing costs.
- Risks of False Negatives: Conversely, missed defects represent a considerable risk, potentially leading to compromised product quality and, in severe cases, patient harm.
- Rigorous System Validation and Calibration: Regular and thorough validation and calibration are essential to maintain both sensitivity and specificity over time. This ensures the system performs within acceptable limits.
- Machine Learning for Improved Classification: Implementing machine learning algorithms allows the system to learn from vast datasets of images, improving its ability to accurately classify defects and reduce false positives and negatives.
Data Management and Analysis in Automated Visual Inspection for Lyophilized Vials
Effective data management and analysis are crucial for optimizing AVI systems and ensuring consistent performance.
- Defect Tracking and Trend Identification: Comprehensive data management allows for thorough tracking of identified defects. This enables the identification of trends and patterns indicative of potential problems in the manufacturing process.
- Process Improvement Insights: Analysis of inspection data can pinpoint areas for improvement within the manufacturing process itself, leading to a reduction in defect occurrence.
- User-Friendly Software for Data Visualization: User-friendly software for data visualization and reporting simplifies the interpretation of complex datasets, allowing for rapid identification of trends and anomalies.
- Integration with MES Systems: Integrating AVI systems with existing Manufacturing Execution Systems (MES) provides a seamless flow of data, improving overall manufacturing efficiency and traceability.
Strategies for Improving Accuracy in Automated Visual Inspection for Lyophilized Vials
Several strategies can significantly enhance the accuracy and reliability of Automated Visual Inspection for Lyophilized Vials. These strategies focus on advanced imaging techniques, artificial intelligence, and process optimization.
Advanced Imaging Techniques
Employing advanced imaging techniques can significantly improve the detection capabilities of AVI systems.
- Higher-Resolution Cameras and Advanced Lighting: Utilizing higher-resolution cameras, coupled with advanced lighting techniques such as structured lighting and hyperspectral imaging, allows for enhanced visualization of subtle defects.
- 3D Imaging Capabilities: Moving beyond 2D inspection, 3D imaging provides a more comprehensive view of the vial and its contents, particularly useful in detecting defects hidden beneath the surface of the lyophilized cake.
- Exploring Alternative Modalities: Exploring alternative imaging modalities such as terahertz (THz) imaging could offer further advancements, providing unique insights into the vial's contents.
- Integration of Multiple Techniques: Combining different imaging techniques provides a complementary approach, leveraging the strengths of each to enhance overall detection capabilities.
Artificial Intelligence and Machine Learning
The application of AI and machine learning algorithms offers a transformative approach to enhancing AVI accuracy.
- Improved Defect Classification: AI and machine learning algorithms can be trained to recognize complex patterns and subtle variations, improving the classification of defects and minimizing false positives and negatives.
- Large Datasets for Robustness: Training these algorithms on large, high-quality datasets significantly improves their accuracy and robustness. This involves collecting and carefully labeling a large number of images of vials with and without defects.
- Deep Learning for Feature Extraction: Deep learning algorithms are especially effective at automatically extracting relevant features from images, identifying subtle variations that might be missed by human inspectors or traditional algorithms.
- Continuous Learning and Adaptation: AI models can continuously learn and adapt over time, improving their performance as more data is processed. This allows the system to adapt to variations in the manufacturing process and product characteristics.
Improved Workflow and Process Optimization
Optimizing the workflow and manufacturing processes themselves plays a critical role in improving AVI accuracy.
- Standardized Vial Handling: Standardizing vial handling and presentation ensures consistent imaging conditions, minimizing variations that can lead to false positives or negatives.
- Robust Quality Control Procedures: Implementing rigorous quality control procedures throughout the manufacturing process ensures that only high-quality images are used for training and validating the AVI system.
- Consistent Vial Presentation: Consistent and controlled vial presentation to the inspection system is crucial for accurate and reproducible results.
- Regular System Calibration and Maintenance: Regular calibration and maintenance of the AVI system are essential to maintain optimal performance and accuracy.
Conclusion: The Future of Automated Visual Inspection for Lyophilized Vials
Improving the accuracy of Automated Visual Inspection for Lyophilized Vials is not simply an enhancement; it is a necessity for ensuring product quality and patient safety. By implementing the advanced imaging techniques, leveraging the power of artificial intelligence, and optimizing workflows, manufacturers can significantly enhance the reliability and precision of their AVI systems. This ultimately translates to reduced waste, increased efficiency, and, most importantly, improved patient outcomes. Investing in and continually upgrading your Automated Visual Inspection for Lyophilized Vials technology is a crucial step towards maintaining the highest standards of pharmaceutical manufacturing. Explore the latest advancements in Automated Visual Inspection for Lyophilized Vials technology to optimize your processes today.
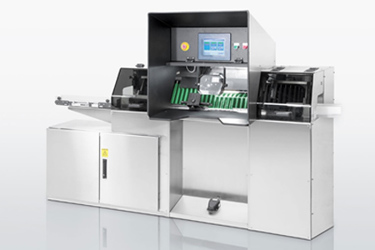
Featured Posts
-
Incident Sa Nojem Boris Dzonson Povreden U Teksasu
May 11, 2025 -
Wildfire Betting A Reflection Of Our Times The Los Angeles Case
May 11, 2025 -
Nba Playoffs 2024 Ta Zeygaria Kai Oi Imerominies Ton Agonon
May 11, 2025 -
2025 Mtv Movie And Tv Awards Officially Cancelled
May 11, 2025 -
The Crazy Rich Asians Tv Show Henry Goldings Role And Fan Reactions
May 11, 2025