Overcoming Hurdles In Automated Visual Inspection Of Lyophilized Drug Products
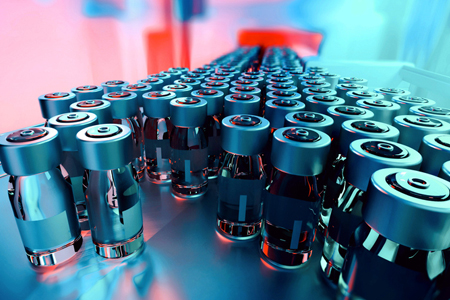
Table of Contents
Image Acquisition Challenges in AVI for Lyophilized Products
The inherent variability in the appearance of lyophilized drug cakes presents a significant challenge for automated visual inspection systems. Consistent, high-quality images are crucial for accurate defect detection.
Variations in Lyophilized Cake Appearance
Lyophilized cakes exhibit considerable visual variability depending on several factors:
- Different lyophilization cycles: Variations in freeze-drying parameters can lead to differences in cake structure and appearance.
- Formulation variations: Changes in drug formulation can impact the cake's physical properties and visual characteristics.
- Product-specific characteristics: Each drug product possesses unique properties that influence the final cake appearance.
Robust image acquisition techniques are essential to minimize the impact of these variations. This includes carefully controlled environmental conditions and potentially utilizing advanced imaging techniques like multispectral imaging.
Lighting and Shadowing Effects
Inconsistent lighting significantly affects image quality, leading to both false positives (identifying defects where none exist) and false negatives (missing actual defects).
- Strategies for optimized lighting: Diffuse lighting, multi-angle illumination, and structured lighting techniques can minimize shadows and enhance image clarity. Consideration of specialized lighting technologies such as LED arrays with adjustable intensity and color temperature is crucial.
- Challenges of shadowing from vial geometry: The cylindrical shape of vials often casts shadows that obscure parts of the lyophilized cake, hindering accurate inspection. Careful positioning of light sources and advanced image processing techniques are needed to mitigate this issue.
Dealing with Reflections and Glare
Reflections from the vial surface and the lyophilized cake itself introduce significant noise and artifacts into images, complicating automated defect detection.
- Anti-reflective coatings: Applying specialized coatings to vials can reduce reflections and improve image quality.
- Polarization filters: These filters can selectively block reflected light, enhancing contrast and clarity.
- Image processing techniques: Advanced algorithms can be employed to identify and remove glare and reflections from the acquired images.
Advanced Image Processing and Analysis Techniques
The success of automated visual inspection heavily relies on sophisticated image processing and analysis techniques capable of handling the inherent complexities of lyophilized drug products.
Algorithms for Defect Detection
Computer vision algorithms are crucial for automated defect detection. These algorithms analyze images to identify deviations from pre-defined acceptance criteria.
- Specific algorithms: Convolutional neural networks (CNNs) and support vector machines (SVMs) are commonly used for their ability to learn complex patterns and classify defects effectively. Deep learning approaches offer particularly powerful tools for handling variations in appearance.
- Training data requirements: The effectiveness of these algorithms heavily depends on the quality and quantity of training data. A large, representative dataset is essential to ensure accurate and reliable defect detection.
Handling Variability and Noise
Noise and variations in image data can significantly impact the accuracy of defect detection. Effective methods are crucial for mitigating this impact.
- Image filtering techniques: Various filters can be applied to reduce noise and enhance image quality prior to analysis.
- Data normalization: This process helps standardize the image data, reducing the impact of variations in lighting and other factors.
- Statistical analysis: Statistical methods can be used to identify and filter out outliers and noise in the data.
False Positive/Negative Minimization
Minimizing false positives and negatives is paramount for reliable AVI.
- Algorithm optimization: Fine-tuning algorithms and adjusting parameters can significantly improve accuracy and reduce misclassifications.
- Rigorous validation: Thorough validation using a large dataset of known good and defective samples is essential to ensure the accuracy and reliability of the AVI system.
- Integration with other quality control methods: Combining AVI with other quality control methods (e.g., weight checks, residual moisture analysis) can improve overall accuracy and confidence in product quality.
Implementation and Validation of AVI Systems
Successful implementation and validation of AVI systems require careful consideration of various factors.
System Integration and Workflow
Integrating AVI systems into existing production lines demands a strategic approach.
- Considerations for system placement: Optimal placement minimizes disruption to existing workflows.
- Data management: A robust data management system is crucial for efficient storage, retrieval, and analysis of inspection data. This often involves integration with Laboratory Information Management Systems (LIMS).
- Integration with existing systems: Seamless integration with existing equipment and software (e.g., MES, ERP) is essential for smooth operation.
Validation and Regulatory Compliance
Validation is critical for demonstrating that the AVI system meets regulatory requirements.
- Qualification activities: This involves demonstrating that the system is fit for its intended purpose.
- Performance verification: This step verifies the system's accuracy, precision, and reliability.
- Ongoing system monitoring: Regular monitoring and maintenance are essential to ensure the continued performance of the AVI system. Compliance with regulations like 21 CFR Part 11 for electronic records and signatures is paramount.
Cost-Benefit Analysis
Implementing AVI systems requires an upfront investment, but the long-term benefits often outweigh the costs.
- Return on investment (ROI): Cost savings from reduced labor costs, improved efficiency, and reduced product waste contribute significantly to the ROI.
- Improved product quality: The increased accuracy of AVI contributes to higher product quality and reduced risk of releasing defective products.
- Enhanced regulatory compliance: A validated AVI system helps ensure compliance with regulatory requirements, mitigating potential risks and penalties.
Conclusion: Optimizing Automated Visual Inspection for Lyophilized Drug Products
Implementing effective automated visual inspection systems for lyophilized drug products presents significant challenges related to image acquisition, algorithm development, system integration, and validation. However, overcoming these hurdles offers substantial rewards. By employing robust image acquisition techniques, advanced image processing algorithms, and rigorous validation procedures, pharmaceutical manufacturers can significantly improve the speed, accuracy, and efficiency of their quality control processes. The resulting improvements in lyophilized product quality, reduced labor costs, and enhanced regulatory compliance make the investment in robust automated visual inspection systems worthwhile. We encourage you to explore the solutions discussed in this article and further investigate the technologies and techniques available to optimize automated visual inspection of your lyophilized drug products and elevate your pharmaceutical quality control strategies. Investing in advanced automated visual inspection systems is crucial for ensuring the highest standards of lyophilized product quality in pharmaceutical manufacturing.
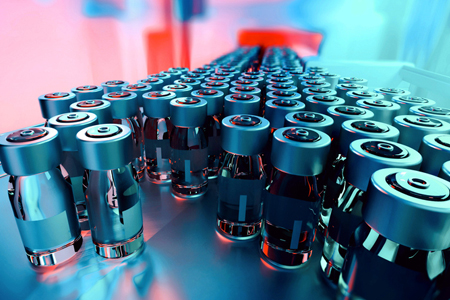
Featured Posts
-
Werder Bremens Victory Over Holstein Kiel A Match Analysis
May 11, 2025 -
Measles Outbreak In North Dakota School Quarantine For Unvaccinated Children
May 11, 2025 -
Fabers Honours Rejection Schoofs Absence From Debate Fuels Speculation
May 11, 2025 -
Porsche 911 Gt 3 Rs 4 0 Performance As Driven By Graham Rahal
May 11, 2025 -
Aaron Judges 1 000 Games Hall Of Fame Trajectory
May 11, 2025