Pentagon Audit Highlights F-35 Inventory Management Failures
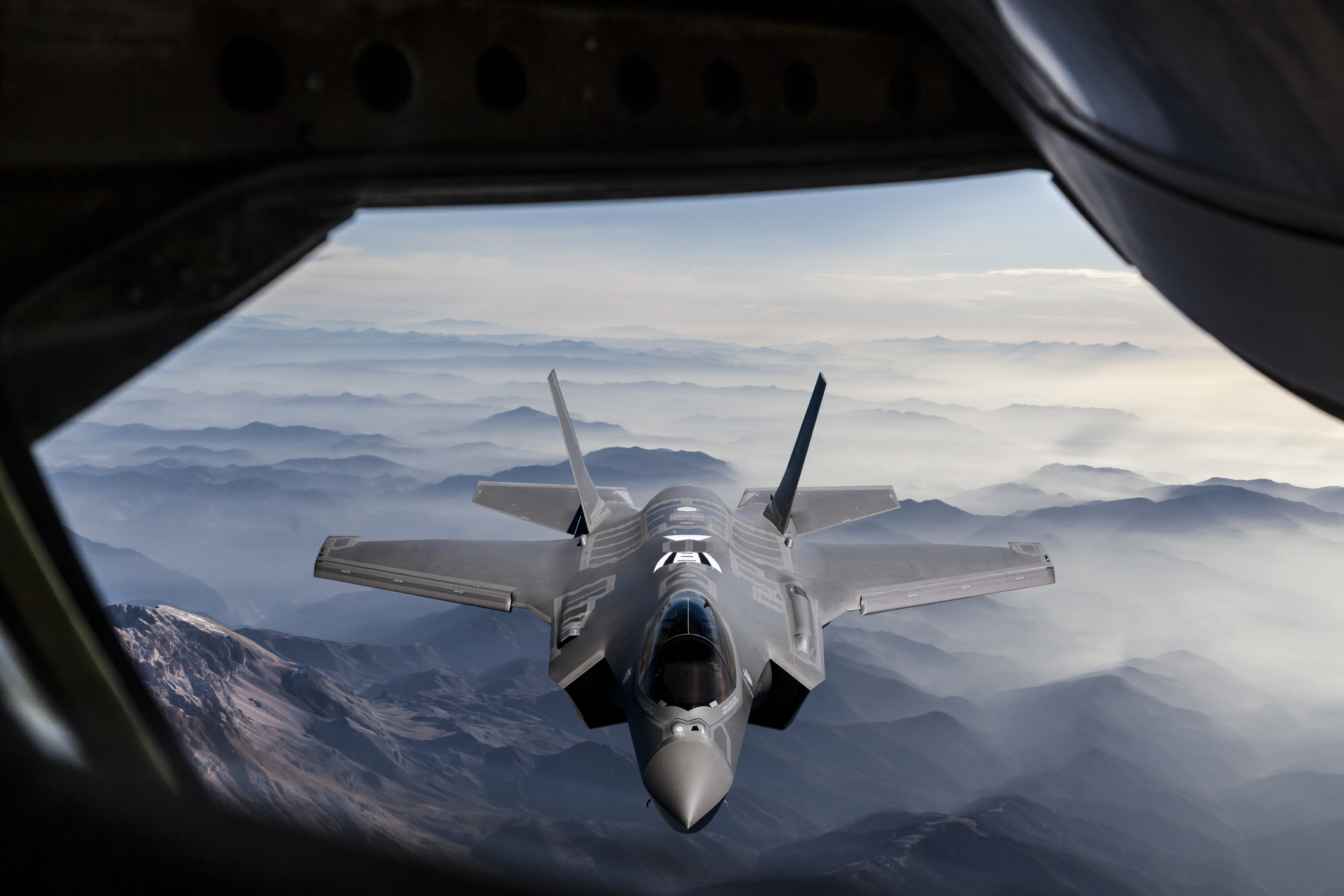
Table of Contents
Key Findings of the Pentagon Audit on F-35 Inventory Management
The audit, whose scope encompassed the entire F-35 supply chain, utilized a combination of data analysis, on-site inspections of warehouses and maintenance facilities, and interviews with personnel involved in F-35 maintenance and logistics. The methodology aimed to assess the effectiveness of current inventory management practices and identify areas for improvement. The findings paint a concerning picture of significant shortcomings.
Specific inventory management failures detailed in the audit include:
- Inaccurate tracking of parts and components: The audit revealed discrepancies between reported inventory levels and actual on-hand quantities, leading to delays in maintenance and repair. This inaccurate tracking significantly impacts the ability to effectively manage the supply chain and predict future needs.
- Difficulties in locating needed parts for maintenance and repairs: The report highlighted instances where essential components for F-35 maintenance were difficult or impossible to locate, resulting in extended aircraft downtime. This points towards systemic issues with part organization and cataloging within the existing system.
- Delays in receiving crucial components, impacting aircraft availability: Significant delays in the delivery of critical parts resulted in a reduction in the number of operational F-35s. These delays are costly, not just financially, but also in terms of compromised military readiness.
- Inefficient warehousing and storage procedures: The audit criticized inefficient warehousing and storage practices, leading to wasted space, increased risk of damage to parts, and difficulties in locating items quickly. Improved storage and organization are key to better inventory management.
- Lack of real-time data visibility across the supply chain: The absence of a unified, real-time inventory management system hampered effective tracking of parts throughout the entire supply chain, from manufacturers to maintenance facilities. This lack of visibility makes accurate forecasting and efficient planning nearly impossible.
The impact of these failures is substantial. The audit estimated significant cost overruns due to delays and inefficiencies, with hundreds of aircraft experiencing extended periods of grounding due to parts shortages. These delays also contribute to program delays, pushing back planned deployments and impacting overall military readiness.
Impact on F-35 Operational Readiness and Maintenance
The inventory management failures directly impact the operational readiness of the F-35 fleet. Insufficient parts availability translates directly into:
- Increased aircraft downtime: The lack of readily available parts means aircraft spend more time in maintenance, reducing their operational availability.
- Reduced flight hours: Grounding due to parts shortages directly translates to fewer flight hours for training and operational missions.
- Higher maintenance costs: Delays and inefficiencies increase labor costs and the overall expense of keeping the F-35 fleet operational.
- Compromised mission capabilities: Reduced operational readiness diminishes the F-35's ability to fulfill its intended missions, impacting national security and defense preparedness. This is a critical concern, particularly given the F-35's strategic role.
Underlying Causes of F-35 Inventory Management Problems
Several factors contribute to the F-35's inventory management woes:
- Complex supply chain involving multiple contractors: The global nature of the F-35 program involves a vast and intricate network of contractors, making coordination and information sharing challenging.
- Lack of effective data integration and information sharing: The absence of a centralized, integrated system for tracking inventory across the entire supply chain hinders effective management.
- Inadequate software and technology for inventory tracking: Outdated or insufficient technology further exacerbates the problems of data integration and real-time visibility.
- Insufficient training and expertise among personnel responsible for managing inventory: A lack of properly trained personnel hampers effective inventory control and management.
Proposed Solutions and Recommendations for Improvement
The audit and subsequent expert analysis suggest several key improvements:
- Implementing a more robust and integrated inventory management system: A centralized, real-time system is crucial for accurate tracking and efficient management of parts across the entire supply chain.
- Investing in advanced technology for inventory tracking and management: This includes implementing advanced software, utilizing barcodes and RFID technology, and adopting predictive analytics.
- Improving data sharing and collaboration across the supply chain: Enhanced communication and collaboration among contractors and military personnel are vital.
- Enhancing training and expertise of personnel: Improved training programs focused on modern inventory management techniques will improve the efficiency and accuracy of the F-35 inventory system.
- Streamlining the procurement process for F-35 parts and components: A more efficient procurement system can minimize delays and ensure timely delivery of essential components.
Conclusion
The Pentagon audit's findings on F-35 inventory management highlight critical vulnerabilities within the program. These failures not only lead to significant cost overruns and delays but also jeopardize the operational readiness of the F-35 fleet, impacting national security. Addressing these issues requires immediate and decisive action to improve inventory management practices. The sheer scale of these problems underscores the urgency for reform.
Call to Action: The future effectiveness and cost-efficiency of the F-35 program hinge on resolving these critical F-35 inventory management failures. Demand accountability from our government and support initiatives that prioritize improved inventory management for our national defense. Learn more about the ongoing efforts to improve F-35 program efficiency and hold your elected officials accountable for addressing these critical issues. Effective F-35 inventory management is not just about cost savings; it's about ensuring national security.
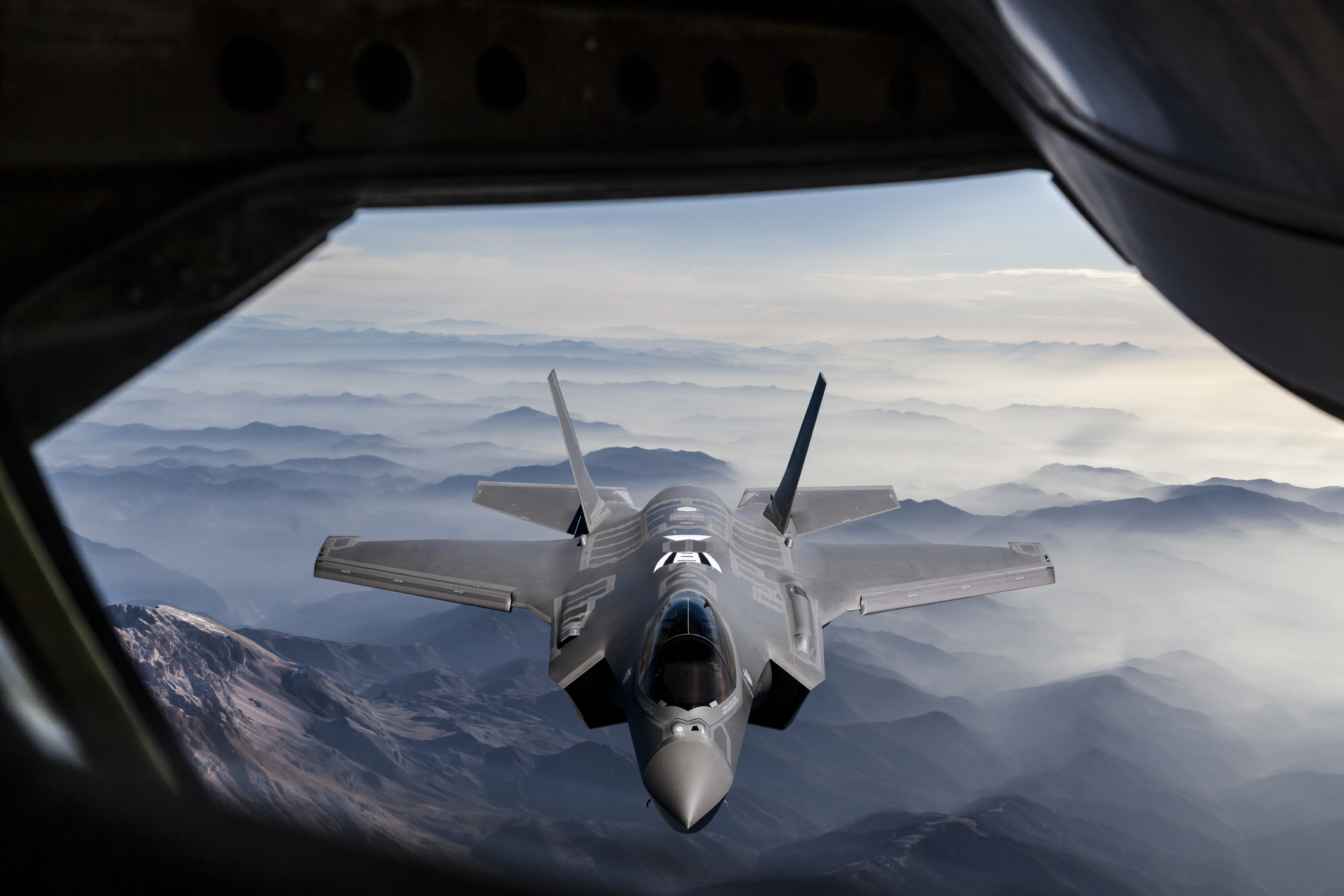
Featured Posts
-
2025 Cruise Ships A Detailed Look At The Biggest Innovations
Apr 30, 2025 -
Hostage Crisis Argamanis Emotional Plea At Time Magazine Event
Apr 30, 2025 -
Did Chris Paul Harrison Barnes And Julian Champagnie Play Every Spurs Game This Season
Apr 30, 2025 -
Ofcom Complaint Filed Over Chris Kaba Panorama Police Watchdogs Concerns
Apr 30, 2025 -
Tina Knowles Beauty Tip Achieving Blue Ivys Perfect Eyebrows
Apr 30, 2025