Practical Solutions For Automated Visual Inspection Of Lyophilized Products
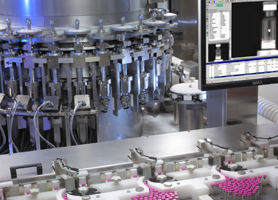
Table of Contents
Challenges in Manual Visual Inspection of Lyophilized Products
Manual inspection of lyophilized products is a labor-intensive and time-consuming process fraught with inherent limitations. These limitations directly impact the speed, accuracy, and cost-effectiveness of quality control.
-
High labor costs and time-consuming process: Manual inspection requires significant personnel time, leading to substantial labor costs and potential production bottlenecks. The sheer volume of products often necessitates large inspection teams, further increasing expenses.
-
Subjectivity and inconsistencies in human visual assessments: Human inspectors, despite rigorous training, may exhibit variations in their assessments. Subjectivity introduces inconsistencies in defect identification and classification, leading to potential quality issues.
-
Difficulty in maintaining consistent inspection standards across multiple inspectors: Ensuring consistent inspection standards across a team of human inspectors is challenging. Variations in interpretation and fatigue can significantly impact the accuracy and reliability of the inspection process.
-
Increased risk of human error leading to product recalls or quality issues: Human error is unavoidable. Missed defects can result in the release of substandard products, potentially leading to costly product recalls and damage to brand reputation.
-
Bottlenecks in production due to manual inspection limitations: The slow speed of manual inspection often creates bottlenecks in the production line, hindering overall efficiency and impacting timely delivery.
Benefits of Automated Visual Inspection Systems for Lyophilized Products
Automated visual inspection systems offer compelling advantages over traditional manual methods, significantly enhancing the efficiency and reliability of quality control for lyophilized products.
-
Significantly improved speed and throughput of inspection: Automated systems can inspect a vastly greater number of vials per hour compared to manual inspection, significantly increasing throughput and reducing inspection time.
-
Objective and consistent assessment, eliminating human subjectivity: Automated systems provide objective assessments, eliminating the inconsistencies associated with human interpretation. This ensures uniform quality control standards across all products.
-
Reduced labor costs and increased overall efficiency: By automating the inspection process, manufacturers reduce their reliance on large inspection teams, leading to substantial cost savings and increased overall efficiency.
-
Enhanced detection of subtle defects often missed during manual inspection (e.g., cracks, discoloration, particulate matter): Automated systems, equipped with advanced imaging and analysis capabilities, can detect even subtle defects that may be easily overlooked by human inspectors. This ensures higher product quality and reduces the risk of releasing defective products.
-
Improved regulatory compliance and traceability through automated documentation: Automated systems generate comprehensive, auditable records of every inspection, simplifying regulatory compliance and facilitating product traceability. This detailed documentation is crucial for meeting stringent regulatory requirements.
-
Real-time data analysis for continuous process improvement: The data generated by automated inspection systems can be analyzed to identify trends and potential process improvements, enabling continuous enhancement of manufacturing processes and quality control.
Types of Automated Visual Inspection Technologies
Several advanced technologies underpin automated visual inspection systems for lyophilized products. The choice of technology depends on the specific needs and requirements of the manufacturing process.
-
Machine Vision Systems: These systems utilize high-resolution cameras and sophisticated image processing algorithms to identify and classify defects. Different camera types, such as high-resolution cameras, multispectral cameras (capable of capturing images across various wavelengths), and 3D cameras, can be employed to meet specific requirements.
-
AI and Deep Learning: Artificial intelligence (AI) and deep learning algorithms significantly enhance the accuracy and adaptability of automated inspection systems. These technologies allow the system to learn and adapt to variations in lyophilized product appearance, improving defect detection accuracy over time.
-
Spectroscopic Imaging: Spectroscopic imaging techniques, such as near-infrared (NIR) spectroscopy, can be used to detect internal defects within the lyophilized product that may not be visible to standard cameras. This provides a more comprehensive assessment of product quality.
Implementing Automated Visual Inspection: Key Considerations
Successful implementation of an automated visual inspection system requires careful planning and consideration of several key factors.
-
System Selection: Selecting the right system involves assessing throughput requirements, the types of defects to be detected, the level of integration with existing equipment, and the budget.
-
Validation and Qualification: Thorough validation and qualification of the automated inspection system are essential to demonstrate its accuracy and reliability. This process must adhere to relevant regulatory guidelines, such as those from the FDA and EMA.
-
Data Management and Reporting: Implementing a robust data management system is crucial for storing, managing, and analyzing the vast amounts of data generated by the automated system. This ensures traceability and supports continuous improvement initiatives. Comprehensive reporting capabilities are necessary for regulatory compliance.
-
Return on Investment (ROI): A thorough ROI analysis should be conducted to evaluate the cost savings associated with reduced labor costs, improved efficiency, and reduced product recalls against the initial investment in the automated system.
Case Studies and Real-World Applications
Numerous pharmaceutical manufacturers have successfully implemented automated visual inspection systems for lyophilized products, achieving significant improvements in quality control. For example, one leading pharmaceutical company reported a 30% reduction in defects and a 20% increase in throughput after implementing an automated inspection system. Another company experienced a significant decrease in product recalls following the integration of an AI-powered automated inspection system, highlighting the substantial benefits of adopting these technologies.
Conclusion
This article has highlighted the limitations of manual visual inspection of lyophilized products and demonstrated the significant advantages of transitioning to automated visual inspection systems. Automated systems offer superior efficiency, accuracy, and regulatory compliance. By carefully considering the key implementation aspects, pharmaceutical manufacturers can greatly enhance their quality control processes, reduce the risk of product recalls, and ultimately deliver higher-quality lyophilized products to patients. Invest in automated visual inspection to optimize your lyophilized product quality control and achieve superior efficiency. Explore the latest advancements in automated inspection technologies and discover how to seamlessly integrate these solutions into your manufacturing process. Contact us today to learn more about automated visual inspection solutions for lyophilized products.
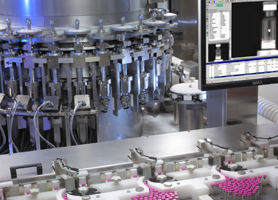
Featured Posts
-
Hertha Bscs Woes Boateng And Kruses Contrasting Perspectives
May 11, 2025 -
Chisholm Vs Judge A Statistical Comparison Of Their Early Seasons
May 11, 2025 -
Tom Cruise And Ana De Armas Spotted Together Again Are They Dating
May 11, 2025 -
Who Will Be The Next Pope 9 Leading Candidates
May 11, 2025 -
Trump Administration Weighs Options To Expedite Nuclear Power Plant Builds
May 11, 2025