U.S. Companies Slash Costs Amidst Tariff Uncertainty
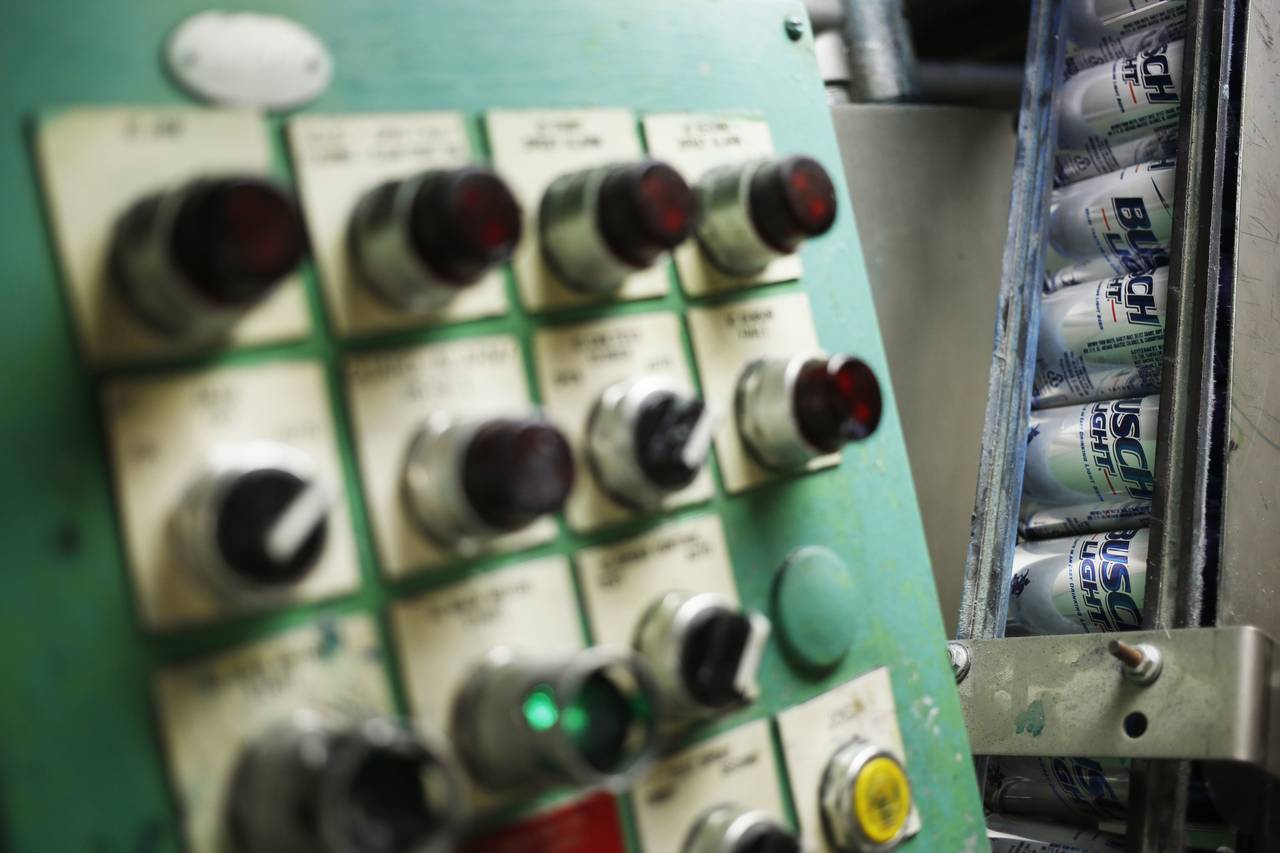
Table of Contents
Restructuring Supply Chains to Minimize Tariff Impact
The fluctuating nature of tariffs has made supply chain optimization a top priority for U.S. companies. Businesses are actively seeking ways to avoid or minimize tariff-related expenses, leading to significant shifts in sourcing and logistics. This involves a multi-pronged approach focusing on several key strategies.
Keywords: Supply chain optimization, tariff avoidance, sourcing, relocation, nearshoring, reshoring, import diversification.
-
Shifting Sourcing: Many companies are actively shifting their sourcing away from tariff-affected countries. This includes:
- Nearshoring: Relocating production to countries geographically closer to the U.S., reducing transportation costs and lead times. Mexico and Canada are popular choices.
- Reshoring: Bringing manufacturing back to the United States, although this option often involves higher labor costs. This strategy is particularly appealing for companies prioritizing domestic production and reducing reliance on foreign suppliers.
- Diversification: Spreading sourcing across multiple countries to mitigate the risk of disruptions from any single location. This approach diversifies risk and potentially reduces vulnerability to tariff increases in any one region.
-
Optimizing Logistics: Companies are also re-evaluating their shipping routes and logistics strategies to minimize costs. This can involve:
- Exploring Alternative Ports: Utilizing less congested ports to reduce delays and associated expenses.
- Negotiating with Carriers: Securing better freight rates and terms through improved negotiation with shipping companies.
- Investing in Technology: Implementing advanced supply chain management software to improve visibility, efficiency, and cost control.
Implementing Cost-Cutting Measures Across Departments
Beyond supply chain adjustments, U.S. companies are implementing sweeping cost-reduction strategies across all departments to maintain profitability in this challenging environment. This involves a comprehensive approach focusing on operational efficiency and strategic budget management.
Keywords: Cost reduction strategies, budget cuts, operational efficiency, workforce optimization, technology investment, process improvement.
-
Operational Efficiency: Streamlining processes, eliminating redundancies, and improving workflow efficiency are paramount. This includes:
- Process Automation: Investing in automation technologies to reduce manual labor costs and improve productivity.
- Lean Management Principles: Adopting lean manufacturing principles to minimize waste and maximize efficiency.
- Consolidating Operations: Combining or closing underperforming facilities to reduce overhead costs.
-
Workforce Optimization: While difficult, workforce adjustments are often necessary. This may involve:
- Hiring Freezes: Temporarily suspending hiring to control labor costs.
- Voluntary Separation Programs: Offering incentives for employees to voluntarily leave the company. This is often a less disruptive alternative to layoffs.
- Retraining Programs: Investing in employee training to enhance skills and improve productivity.
-
Budgetary Control: Stricter budgetary controls and enhanced financial monitoring are crucial. This includes:
- Regular Budget Reviews: Frequent reviews of budgets to identify areas for potential cost savings.
- Cost-Benefit Analysis: Thorough analysis of all expenditures to ensure value for money.
- Negotiating with Vendors: Renegotiating contracts with vendors and suppliers to secure better pricing and terms.
Navigating Financial Risks and Uncertainty
The economic uncertainty created by tariff fluctuations necessitates a proactive approach to financial risk management. Companies must develop robust strategies to protect their financial stability and maintain liquidity.
Keywords: Financial planning, risk management, hedging strategies, investment decisions, capital expenditure, liquidity management.
-
Hedging Strategies: Implementing hedging strategies to mitigate the impact of currency fluctuations and price volatility is vital. This can involve:
- Currency Hedging: Using financial instruments to offset potential losses from currency fluctuations.
- Commodity Hedging: Protecting against price volatility in raw materials and other commodities.
-
Capital Expenditure Management: Careful review and adjustment of capital expenditure plans are crucial. This involves:
- Prioritizing Essential Projects: Focusing investment on essential projects that directly contribute to profitability and long-term growth.
- Delaying Non-Essential Investments: Postponing or canceling non-essential capital expenditures to conserve cash.
-
Liquidity Management: Maintaining sufficient cash flow and liquidity is paramount. This includes:
- Improving Accounts Receivable: Efficiently managing accounts receivable to accelerate cash collection.
- Strengthening Supplier Relationships: Negotiating favorable payment terms with suppliers to extend payment deadlines.
- Seeking Government Support: Exploring available government support programs and financial assistance to mitigate the financial impact of tariffs.
The Impact on Small and Medium-Sized Enterprises (SMEs)
Small and medium-sized enterprises (SMEs) are particularly vulnerable to the effects of tariff uncertainty due to their limited resources and capacity for adaptation. The impact can be severe, potentially leading to financial instability and business closures.
Keywords: SMEs, small businesses, tariff impact on small businesses, financial vulnerability, government support for small businesses.
- Limited Resources: SMEs often lack the resources and financial reserves to effectively implement the cost-cutting strategies employed by larger corporations.
- Access to Finance: Securing financing can be challenging for SMEs, making it difficult to navigate financial uncertainties.
- Government Support: SMEs are heavily reliant on government assistance programs and support initiatives to mitigate the negative impacts of tariff uncertainty.
Conclusion
The uncertainty surrounding U.S. tariffs is forcing a significant restructuring of business operations across various sectors. Companies are responding with aggressive cost-cutting measures, from reshaping their supply chains to implementing significant internal efficiencies. Understanding these changes is crucial for navigating the ongoing economic volatility. The impact on SMEs is particularly noteworthy, highlighting the need for targeted government support and proactive adaptation strategies.
Call to Action: Stay informed on the latest developments impacting your business and proactively develop strategies to mitigate the effects of tariff uncertainty. Learn more about effective cost-cutting strategies for your U.S. company and adapt to the changing economic landscape. Don't let tariff uncertainty cripple your business – take control and implement proactive strategies for managing costs and navigating this challenging economic climate.
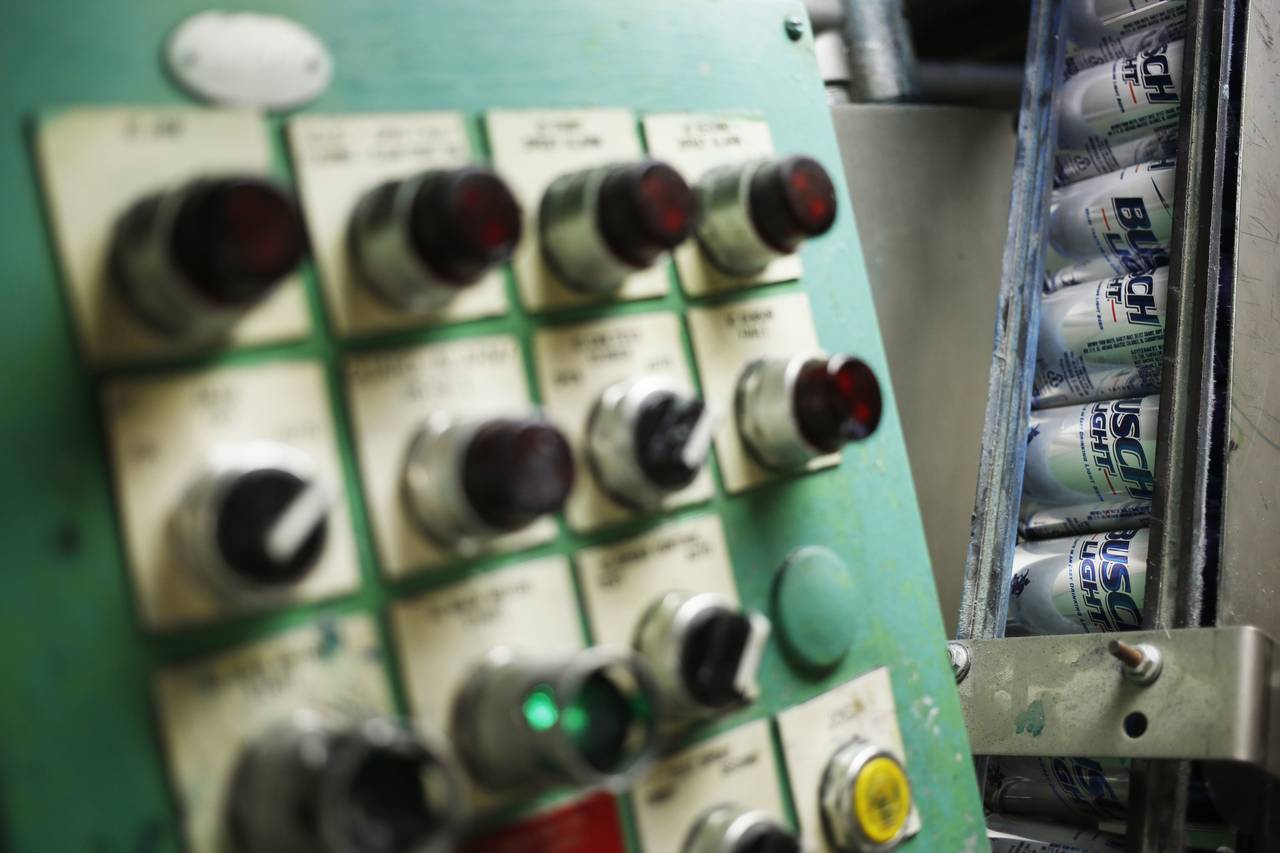
Featured Posts
-
Capital Summertime Ball 2025 Everything You Need To Know About Getting Tickets
Apr 29, 2025 -
Why Older Viewers Are Choosing You Tube For Their Entertainment
Apr 29, 2025 -
Willie Nelson And Familys Austin City Limits Show Highlights And Memories
Apr 29, 2025 -
Nyt Spelling Bee Solutions For March 13 2025 Find The Pangram
Apr 29, 2025 -
Jancker Und Klagenfurt Investor Sucht Nach Loesungen Im Bundesliga Abstiegskampf
Apr 29, 2025